Logistics operations are the circulatory system of any brand. Without them, companies could not move the lifeblood of their business – products – from Points A to B and get them in the hands of customers. However, in recent years the business landscape has grown in scope and complexity, presenting a variety of new challenges for logistics managers. As a result, companies should look to supply chain logistics software for more visibility, flexibility, and control, and ensure that they can keep their “circulatory system” in good health.
With so many options on the market, choosing the best solution for your business can be tough, and given the crucial role that these platforms play in managing operational efficiency, some homework is required to make the right decision. This post will guide you through the key factors to consider when evaluating logistics software to help you make an informed decision that aligns with your organization’s unique needs and goals. From scalability and integration capabilities to user-friendliness and ROI, we’ll cover the key differentiators that separate the best-in-class supply chain logistics software from other vendors.
Types of Supply Chain Logistics Software
Logistics refers to the coordination and oversight of activities involved in moving goods from point of origin to point of consumption. At the tactical level, logistics management encompasses a wide range of functionalities, from inventory management and warehouse optimization to transportation planning and demand forecasting.
Logistics software platforms provide the digital infrastructure that is transforming supply chains for a new era of commerce. From transportation forecasting to logistics visibility, these solutions help companies gain real-time visibility into shipments, improve response time during disruptions, and make it easier to collaborate and coordinate with partners and customers. As supply chains grow increasingly complex and global, these specialized software solutions are helping businesses take more control of their logistics operations.
Let’s explore some examples of supply chain logistics software and what types of benefits these platforms provide.
Transportation forecasting and planning
Demand planning and transportation forecasting help companies anticipate future needs and adapt their strategies accordingly. Demand planning tools analyze and forecast demand using historical sales data, market trends, seasonality, and economic volatility. However, in recent years the vulnerabilities of this model have come to light in a way that has pushed the industry to evolve its thinking around planning and forecasting.
In times of constant volatility, relying on historical data may not provide the level of accuracy required to keep up with modern commerce. A newer planning and forecasting solution known as demand sensing leverages artificial intelligence (AI) and machine learning (ML) to analyze data in real time, determine the influence of multiple demand signals, and create accurate daily forecasts for every item at every location. The work that AI/ML can do in seconds might take a human several hours or even days to complete. With more accurate forecasts companies can then make data-driven decisions regarding inventory, production, and resources.
When equipped with better demand planning and forecasting tools, companies can better adapt to disruption in the markets in real time for a more flexible and responsive supply chain.
Inventory and transportation management
Two of the most important variables in logistics management are goods that are moving (because they are in transit), or goods that are not moving (because they are in storage). Either way, there are significant costs associated with both static goods and goods in motion.
When it comes to goods in storage, companies want to reduce their costs by optimizing stock levels. End-to-end logistics management software streamlines order fulfillment, enhances forecast accuracy, and provides real-time visibility into inventory levels, resulting in fewer stockouts. Integrated cross-dock and warehousing functionality allows logistics service providers (LSPs) to manage all multimodal transportation needs and temporary storage requirements for one shipment, documented on one itemized customer invoice. Additional features such as automatic re-ordering can decrease a company’s reliance on manual labor. These features help businesses ensure that their inventory is optimized, while simultaneously reducing carrying costs and ensuring products are available to meet customer demand.
So, now that you’ve managed your static inventory, what about your goods in motion? Transportation managers are also in the business of decreasing costs, and a transportation management system (TMS) allows them to leverage automation for previously manual tasks, such as route optimization, load consolidation, and selecting the most cost-effective shipping methods. Industry-leading TMS solutions also allow real-time tracking and status updates, so companies and customers alike can pinpoint exactly where goods are in their journey. This degree of control and visibility helps businesses cut costs, improve on-time deliveries, and optimize the overall customer experience.
Enhanced visibility into order fulfillment and processing
Visibility into order fulfillment and processing gives companies more control over the journey from customer order to delivery. The moment an order is placed, purchase order collaboration software begins automating and optimizing processes to ensure maximum transparency and efficiency. The software allows users to check inventory availability, prioritize orders based on factors such as shipping method and destination, and create optimized pick lists for warehouse staff. It also orchestrates packing and shipping operations, including managing the collection of items from inventory, selecting the best carrier options and shipping methods, and generating shipping labels and customs documents, if necessary.
When an order reaches the fulfillment stage, the software updates inventory in real time, sends shipment tracking information to the end customer, and provides updates throughout the delivery process. Post-fulfillment, the platform provides analytics and reporting, calculating performance metrics such as order accuracy and processing time, and uses data collected to help companies adapt and improve wherever necessary. By providing more visibility, supply chain logistics software significantly reduces processing times, minimizes errors, and improves overall efficiency, ultimately leading to faster deliveries and higher customer satisfaction.
Carrier management
Most global shippers use multiple carriers, and many still rely on manual booking requests and shipping instructions, making them vulnerable to human error. Automated booking software removes the hassle of multi-party, multi-tier interactions by centralizing control of these processes onto one platform and leveraging automation to save time and reduce errors. Booking software allows companies to share documents and instructions electronically, gives insight into available routes and carriers, and lets them book or tender directly with carriers.
Speaking of manual processes, many companies also still rely on manual processes to pay their carriers. Audit and settlement software automates the entire carrier payment process, allowing companies to compare itemized charges, identify discrepancies, set deviation limits, and pay invoices electronically. As a result, talent is free to devote attention to more strategic tasks.
Logistics teams face a variety of challenges, such as large shipment volumes, rising costs, dwindling resources, sustainability demands, and supply chain disruptions. When considering the last mile leg, vehicle routing and scheduling software, helps companies update and optimize their planning, loading, and routing processes in real time. From one central dashboard, a logistics manager can optimize routes, choose the best drivers for the job, collaborate more effectively, deal with exceptions or disruptions, and track performance – all of which leads to an improved customer experience.
Equipment management
Equipment costs can quickly become a problem for logistics service providers, especially if the equipment in question is missing, off track, or sitting idle. When hundreds of containers have just been emptied, they either need to be returned to action or retrieved by drivers. By leveraging automation, an equipment management tool can help companies reduce empty miles, make better use of discharged import containers, and reduce the risk of fines and penalties. The software can also automate requests for equipment drop-off and pick-up, improving efficiency and lowering a company’s carbon footprint.
Key features of supply chain logistics software
Whether you’re in the market for a focused solution or a digital overhaul of your entire logistics operation, it’s important to understand how the key features of these solutions match up against your biggest challenges. Many solutions offer capabilities such as transportation management, forecasting, vehicle routing, and supply chain traceability, but ultimately, companies must evaluate how compatible a certain solution is with their existing people, processes, and platforms.
So, let’s take a look at some of the key features of supply chain logistics software and talk about the criteria around them.
Analytics & reporting
Analytics provide valuable insights that allow companies to make strategic logistics decisions. These insights are based on vast amounts of data collected from touchpoints across all logistics activities, including sales, inventory, costs, performance, and more. Advanced analytics use AI and ML to identify patterns unseen by the human eye and can help users predict trends or identify issues or risks hidden within the supply chain.
When it comes to reporting, supply chain logistics software utilizes a customized dashboard to present all this information in a user-friendly way. The dashboard allows users to track key performance indicators (KPIs) in real time, such as order fulfillment rates, inventory turnover, and on-time delivery performance. The immediacy of these tools helps managers to quickly identify issues and make data-driven decisions on the fly. Scenario planning is another crucial element of reporting, as it allows companies to model a “digital twin” of their supply chain and stress test it against different scenarios to gauge potential impact. Turning complex data into actionable insights helps companies constantly improve their logistics operations to increase efficiency, reduce costs, and maintain the desired level of customer satisfaction.
Integration Capabilities
Implementing a new enterprise-wide software platform can be a daunting task. Integration capabilities are crucial, as they allow seamless communication and data flow between different systems and stakeholders across the supply chain. A well-integrated system can connect various components such as Enterprise Resource Planning (ERP) systems, Customer Relationship Management (CRM) tools, Transportation Management Systems (TMS), and Warehouse Management Systems (WMS). This interconnectedness eliminates data silos and ensures that all parts of the organization are working with the same, up-to-date information and are all aligned to the same goals.
The ability to integrate with systems outside of your company’s four walls is equally important. The software must play nice with suppliers’ inventory systems, carriers’ tracking platforms, and customers’ order management systems. These integrations enable real-time data exchange, allow for the automation of time-consuming manual processes, and provide unparalleled, end-to-end visibility across the entire supply chain. For example, integration with e-commerce platforms can automatically sync order information, while integration with financial systems can streamline invoicing and payment processes. Ultimately, robust integration capabilities in supply chain logistics software lead to increased efficiency, reduced errors, better decision-making, and improved responsiveness to market changes and customer demands.
How to select the best supply chain logistics software for your business
When it comes to logistics software, there are many options available on the market today. As you begin your buying journey, it’s crucial to consider your specific current needs, challenges your company is facing (or may face in the future), and any growth or expansion plans that might change the scope of your needs. Here are some key criteria and processes to follow make sure you have all the information you need to find the right vendor for your business.
Choosing the right platform
Enterprise Resource Planning (ERP) Systems
Enterprise Resource Planning (ERP) systems are comprehensive software platforms designed to streamline and consolidate core business processes across the breadth of an entire organization. These systems typically include applications for managing several aspects of the business at once, including finance and accounting, human resources (HR), manufacturing, customer relationship management (CRM), and inventory management.
By centralizing data, ERP systems provide a single source of truth for business information. These platforms facilitate collaboration and real-time data sharing between teams and departments, leading to better decision-making and increased efficiency. They are best applied to large organizations with complex, interconnected business processes that are looking to bring all of these various functions under one proverbial umbrella.
ERPs can also vastly improve visibility across departments and standardize processes and reporting. This is especially useful in logistics, as this particular function of the supply chain is interconnected with many others, such as supply, planning, and global trade. However, ERPs often require a long, complicated, and costly implementation process. Still, while ERP implementation has its initial challenges, many businesses have come to realize that the long-term benefits outweigh the initial investment.
Best-of-Breed Solutions
As opposed to ERPs, best-of-breed solutions are specialized software applications that focus on excelling in one specific area of supply chain management, such as transportation management, inventory management or supplier relationship management. They provide robust functionality and advanced features, but only within their specific domain.
There are many benefits to implementing a singular, best-of-breed solution as opposed to a comprehensive ERP. Their specialized nature means they can provide valuable, industry-specific features rather than broad functionality. They are updated more frequently than ERP modules and have more intuitive interfaces, due to their focus on one area of expertise. They are also easier to implement and replace than a full ERP system, providing a level of flexibility that ERPs may not be able to match. With their narrow focus, best-of-breed solutions tend to provide immediate value.
However, there are some considerations to take into account with best-of-breed logistics solutions. They may require significant up-front investments in integration and staff training. Data integrity may suffer when maintained across multiple systems with different interfaces and functionality. And while singular solutions are much more affordable than full ERPs, the total costs of adding piecemeal supply chain logistics software to a company’s digital portfolio can start to add up.
Like any technology investment, companies should consider their needs, scope, and strategy first. Companies that require unique or complex functionality are a good fit for these solutions. Same goes for companies in industries that require specialized supply chain needs, such as pharmaceuticals, technology, or perishables.
Cloud-Based vs On-Premises Systems
Cloud-based solutions offer some significant advantages over on-premises solutions. They are hosted remotely and accessed over the internet, which means lower up-front costs and subscription-based pricing models. These subscriptions typically include automatic updates and regular maintenance. Cloud-based solutions are also scalable and flexible, allowing for rapid growth or change at the enterprise level. And because of their remote nature, they provide easier collaboration and access, especially for teams based across several different geographies and time zones. Since the data and processes contained within them are synced in real time, they are ideal for the logistics space, where time is of the essence and decisions need to be made at speed.
However, cloud-based systems are not without their challenges. There are some security concerns due to their online nature, especially with regard to the remote storage of data. Furthermore, internet or power outages may render these systems unusable for a time. Companies considering cloud-based solutions should strongly consider data security requirements and necessary features before making a decision.
Key Considerations & Criteria
Start by assessing your current logistics processes and identifying pain points or areas for improvement. Consider the scale of your operations, the complexity of your supply chain, and your budget. It’s important to choose a solution that not only addresses your current requirements but also has the flexibility to adapt as your business grows or your needs change.
For a supply chain software platform, there are three primary criteria to evaluate:
- The software’s functionality across various logistics processes
- Its integration capabilities with your existing systems
- The quality of its analytics and reporting tools
These criteria are the meat and potatoes of your logistics platform, and they represent the three features most companies require from supply chain logistics software. However, there are secondary considerations to take into account as well.
The user experience and user interface (UX/UI) are also crucial. The software should be intuitive enough for your team to seamlessly merge the platform and its features into their workflow. Additionally, consider the vendor’s reputation, support services, and track record in your industry. Cloud-based, connected supply chain solutions often offer advantages in terms of accessibility and scalability, but it’s important to verify that they meet your security requirements. Finally, don’t underestimate the importance of a strong implementation plan and ongoing support from the vendor to ensure you get the most value from your investment.
Vendor Selection & RFP Process
Choosing a vendor can be complicated and time-consuming, so a strategic approach is more likely to get you exactly what you are looking for. This means you will have some work to do before, during, and after the sales pitch, but here are three ways to ensure you are as prepared as possible:
Before:
Start by thoroughly assessing your current state of supply chain affairs. Identify existing pain points and define clear objectives for your desired state. Next, create a shortlist of potential vendors based on a combination of research, industry recommendations and recognition, referrals from colleagues, word-of-mouth, etc. Once your shortlist is ready, reach out to your preferred prospects and request a demonstration.
During:
From the get-go, be direct about your needs, expectations, and concerns. Show up to your demo with a list of specific scenarios and questions unique to your business and industry. If possible, ask to interact with the tool yourself during the demo and get a feel for it. How simple or complex is the UX/UI? Is it intuitive? Can you see yourself using the software day in and day out? Be wary of over-promises at this stage, as the salespeople are trying to close the deal. It helps to ask about specific scenarios you’ve encountered or might encounter. If the salesperson can’t address your concerns definitively, chances are they are probably not up to the task.
After:
Don’t hesitate to ask for customer references, especially within your industry or for companies of similar size to yours. Request detailed proposals that outline costs, implementation timelines, and ongoing support. Remember that you’re not just buying software, but also entering a long-term partnership. Evaluate the cultural fit between your organization and the vendor, as this can significantly impact the success of the implementation and ongoing use of the software. Finally, don’t rush the decision – take the time to thoroughly evaluate your options and involve key stakeholders in the process to ensure you choose a solution that will truly meet your business needs.
Comparison shopping can be tedious, but not nearly as tedious as paying for and enduring the wrong vendor partnership or solution. Technology has become the backbone of modern logistics operations, and with so much riding on the ability of your logistics teams to deliver, the choice is not one to be taken lightly.
Upgrade your existing supply chain logistics software with a proven leader
Perhaps one of the most important considerations when shopping for logistics software is expertise. All of the bells and whistles in the world may not be worth it if the vendor developing the platform isn’t familiar with your business, your industry, and the risks and opportunities hidden within your logistics operations.
E2open has been recognized as an industry leader for precisely this reason. For over twenty years, e2open has been developing a connected supply chain platform that consolidates the management and execution of every function of the supply chain – including channel, planning, global trade, logistics, and supply – onto one platform. This blog may be about logistics, but cross-functional collaboration and decision-making are where supply chains are made or broken.
Here are three ways e2open can help streamline your logistics operations for the present and the future.
A trusted industry leader in logistics
In addition to e2open’s pedigree in the supply chain, our team consists of experts with years of experience – not just in supply chain, but in all of the industries served by supply chains as well. Whether you’re in industrial manufacturing, retail, food and beverage, pharmaceuticals, or semiconductors, there’s a good chance we know what “good” looks like in your field. In fact, some of the biggest brands in the world have entrusted e2open with their global logistics needs. After all, e2open pioneered the concept of sub-tier collaboration and is the category creator for advanced planning, trade, channel, and logistics practices, and led the way in integrating AI into the supply chain.
However, some companies simply do not have the bandwidth or resources to handle their logistics activities in-house. By outsourcing operations to our Logistics as a Service (LaaS) team, companies can reduce transportation costs and improve customer service. LaaS from e2open offers the best-in-class strategic supply chain skills of almost 300 logistics coordinators, analysts, managers and engineers, all leveraging the functionality of e2open’s comprehensive suite of logistics applications. With a 10-year average shipper partnership tenure and a commitment to cost savings year-over-year, our LaaS team offers a dependable alternative to hosting an in-house logistics team.
A connected network platform
E2open connects you to the world’s largest business network, bringing together the entire value chain to make, move, and sell your products and services, from internal operations to tier 1 and sub-tier ecosystem partners. We’ve cultivated a network of over 50,000 transportation and logistics partners that offers flexibility in times of crisis, and also provides logistics managers with a deeper pool of data to pull from. Access to e2open’s broad network of trading partners allows for faster onboarding of new suppliers and customers, easier partner integration, and streamlined communication between companies and their suppliers and customers.
Integrated and value-driven applications
E2open introduces true cross-functional collaboration into your supply chain with a platform of best-in-class, connected solutions, working together right out of the box. Our connected supply chain solution consolidates all your planning, logistics, global trade, channel, and supply management needs on a single, connected network platform.
With unified and integrated applications, your business can do more with fewer vendor platforms, simplifying enterprise architecture, reducing integration complexity, and lowering the barrier to transformation. Our connected platform makes it easier for you to make connected decisions that work together across functional boundaries and parties for superior outcomes.
When it comes to upgrading logistics, there’s no time like the present
It’s no secret that the digital transformation of the logistics industry has been a game changer. In the 21st century, we’ve seen the proliferation of logistics software solutions as more and more companies realize that they are a necessity in the digital age. With changing consumer preferences, supply volatility, evolving regulations, growing sustainability demands, and the ever-present threat of another global disruption placing more and more pressure on logistics operations, companies that are slow to evolve will be left behind.
If you are interested in mission-critical, enterprise-grade, secure, and scalable logistics solutions, contact e2open today to learn more.
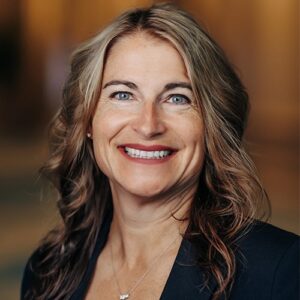
Author
Nicole Hudson
As a Director of Product Marketing at e2open, Nicole is focused on Transportation and Logistics applications. Over her 20+ year career, she has held various positions in product management and product development for supply chain and logistics companies, including JDA and BluJay Solutions. She joined the product marketing team at e2open in 2022 with the BluJay acquisition. Nicole currently lives in WI and enjoys attending her kids’ volleyball and basketball games and traveling in her spare time.