At a high school science fair, a student proceeded to put five metronomes on a single piece of wood. As each metronome was started, the metronome needles bounced back and forth, independent of the others and definitely not in synch. “Behold,” the student said as she placed the platform of metronomes across two cylinders. Within a minute, all five metronomes followed the same tempo in complete synchronization.
Having a single platform for all five metronomes wasn’t the only thing that got them in sync; it also required balancing the entire platform to get each independent metronome to work in synchronicity with the rest of them.
Why is supply chain synchronicity so important?
Companies today can only dream of synchronicity like this. The challenges surrounding the synchronization of functional supply chain silos, such as supply, planning, logistics, global trade, and distribution channels, can all be attributed to a lack of communication, coordination, and collaboration.
As the world transforms, companies can no longer rely on how the supply chain worked in the past. Their processes have been forced to change, and more importantly, their company has had to transform. They are now hit from all sides with disruptions to their supply chain and impacts on their ability to operate efficiently, and they must continue to do more with less.
Political and economic unrest, weather anomalies, and the profound changes in all aspects of the workforce have made it difficult for companies to truly define and execute a supply chain synchronization strategy. These optimization strategies have been the savior during recent supply chain struggles, and leading strategies focused on communication, coordination, and collaboration will continue to carry companies through this fog of the unknown.
The three Cs: communication, coordination, and collaboration
Some of the biggest companies and industries in the world are shifting to a more strategic approach to how they see their supply chain, and as a result, many are finding new solutions to new problems. A strategy of supply chain synchronization leads this shift, and this strategy has three main components:
- Communication – a fully connected supply chain enabling fully-orchestrated communication with all suppliers across all tiers of the supply chain
- Coordination – the ability to coordinate activities and remediation plans with all partners involved in the incident to drive fast remediation
- Collaboration – a forum for all partners to discuss goals and forecasts to ensure all activities align with the most efficient solution
Like the metronomes in our example, true synchronicity requires balance. There are many case studies of companies that have found success in synchronizing their supply chains by utilizing an end-to-end platform that gives equal weight to every function and tier, connecting the entire supply chain and allowing the entire operation to move as one.
Navigating inventory and supply challenges
The challenges currently shocking the automotive manufacturing industry include unprofitable and volatile inventory levels, the need to make assumptions for a feasible supply plan, and a lack of visibility into future requirements for suppliers. These issues have led to increased operating and production costs from maintaining buffer stocks and taking remedial actions to cover volatile demand.
By ensuring optimal inventory levels for all stocked components at the original equipment manufacturer (OEM) and key tier suppliers and utilizing e2open’s supply applications to communicate production requirements and supplier capabilities, an automotive manufacturer was able to achieve a collaborative level of visibility and address gaps immediately in the supply chain as they arise, both upstream and downstream.
By defining priorities across multiple tiers and actively managing supplier capacity through deep, sub-tier collaboration, the automotive industry can ensure that the right demands are met at the right time. Implementing these solutions produces a more accurate and reliable supply plan based on up-to-date information, ultimately reducing costs and improving supply chain efficiency.
Getting everyone on the same frequency
The automotive industry isn’t unique with its supply chain challenges, changes, or disruptions. A multi-billion-dollar consumer and industrial video and radio systems manufacturer also experienced similar disruptions within their multi-tiered supply chain. Tackling their challenges required a similar solution that involved enabling deep collaboration with suppliers across multiple tiers and facilitating rapid “what-if” planning scenario modeling to respond to disruptions in demand, contract manufacturer capacity, or component supply.
Their advanced supply planning solution allowed the brand owner to create clear-to-build plans for contract manufacturers. Meanwhile, the “what-if” planning scenario modeling helped mitigate component shortages and create clear-to-build plans while considering the impact on revenue goals, cost, working capital (inventory), and customer service (fill rate/on-time delivery), significantly increasing internal alignment and external supplier collaboration discussions.
Synchronicity unlocks the true potential of your supply chain
To navigate this transformation successfully, companies must adopt effective supply chain synchronization strategies characterized by complete communication, extended coordination, and deep collaboration. Sub-tier and multi-tier supply collaboration are essential in building strong supplier relationships and fostering supply chain resilience, flexibility, and sustainability. This level of communication allows for effective coordination and collaboration across all stakeholders.
Going back to our metronome example, sub-tier supply collaboration is that set of cylinders on which the platform of metronomes sits. In much the same way, e2open’s Supply suite of applications enables full synchronization across all functional areas. And when your supply chain is in sync, so is the rest of your business.
Who is e2open?
E2open is the connected supply chain software platform that enables the world’s largest companies to transform how they make, move, and sell goods and services. With the broadest cloud-native global platform purpose-built for modern supply chains, e2open connects more than 400,000 manufacturing, logistics, channel, and distribution partners as one multi-enterprise network tracking over 15 billion transactions annually. Our SaaS platform anticipates disruptions and opportunities to help businesses improve efficiency, reduce waste, and operate sustainably. Moving as one.™ You can learn more by reaching out to our experts.
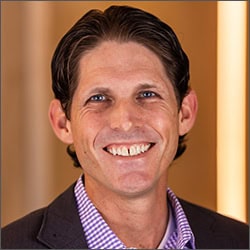
Author
Jeff Eckel
As Director of Product Marketing for e2open, Jeff Eckel is focused on solutions that help clients collaborate across all tiers of supply and manufacturing. With over 20 years of experience in supply chain business intelligence, Jeff has a deep understanding of supply chain management business processes. He specializes in translating complex business challenges into an end-to-end understanding of tangible business value. In his career, Jeff has held a variety of roles including product marketing, product management, solution consulting, and professional services. He is located in Austin, TX, and enjoys spending time with his kids outside of work.